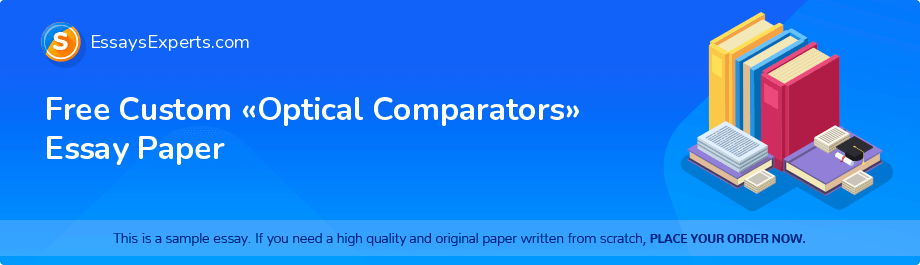
Table of Contents
Optical comparators are instruments that project a magnified image or profile of a part on to a screen to enable it to be compared to a standard overlay profile or scale. They are non-contact devices that function by producing magnified image of parts or components. The images of the parts and components to be measured are displayed on a glass screen using illumination sources, lenses and mirrors. The device unlike the micrometers can make 2-D measurements.
The History of Optical Comparators
Optical comparator was first invented in the early 20th century and specifically in they year1922 by James Hartness. The first optical comparator was known as shadow graphs and was used to project the shadow of a physical object onto a projection screen placed a few feet away (Kulkarni, 2009). The physical object was then compared with the chart showing acceptance levels for that part. The main purpose of the invention was the need to standardize screw thread sizes. It was quickly developed to a one integrated machine that could be placed on top of the bench while in use making it widely known as a bench-top comparator.
The device then underwent a series of developments like the introduction of the automobile edge detection in 1960s and that of readouts in 1970s which made it be more automated. In 1990s, incorporated software became standard optical comparator equipment. Today, computers have been interfaced with optical comparators to enable the running of image analysis. This has made it possible to transfer points from manual or automated edge detection to an external program where they can be directly compared to a CAD data file (Kulkarni, 2009).
The Function of Optical Comparator
The major function of the device is to amplify the inspected materials onto projected screen to allow for their measurement to be taken. Optical comparators were also used to examine wear of a part as well as for set up phases for manufacturing by the late 1920s. In the 1940s, optical comparators were widely used to manufacture nearly every part used in the World War II. This was triggered by its adoption by U.S as a standard its artillery specifications. The comparators became frequent inspection instruments in artillery production and were widely used to measure, gauge, test, and inspect or examine parts for compliance with specifications.
With the introduction of the automobile edge detection in 1960s, the device could now be used to determine the part edge without the input of the operator. With the introduction of the digital readouts in 1970s, the machine became more automated and was used in programmable functions. Today, the optic comparators are increasingly being used in small parts manufacturing plants which produce objects like razor parts and tooth brushes.
Its measure
The screens of optical comparators vary in length. The diameters of the small units may measure between10”-12” while the larger units may measure up to 36”-40” diameter. The larger screen sizes are also available on specialized units. In addition, there are also handled devices with smaller screens as would be expressed.
Cost
Because of their ease of use and their ergonomic designs which help reduce the inspection time, optical operators save time. The costs associated with parts handling and setup times are also significantly reduced because comparators generally allow parts to be held in one orientation for each 2-D view (Davis, 2003). Optical comparators are also general-purpose measurement devices, easily adaptable to design changes and appropriate for either first-article or repetitious inspections. The optical comparator is also an ideal for dimensioning techniques designed to give more leeway to parts in relation to their true functional purpose.
Advantages of Optical Comparators
Unlike the micrometers that provide no external viewpoints, comparator’s screen can be simultaneously viewed by more than one person. The device can be used as a medium for discussion like in facilitating a conference. Second, optical comparators allow quick and simple way of gathering a great amount of information about the part being measured. This is achieved simply by looking at the image on the screen (Davis, 2003). Third, optical comparators can provide more information than just simple dimensions provided by micrometers. The device is able to detect imperfections such as burrs and scratches. Forth, the device can measure in 2-D space. It also makes it possible for length and width to be measured simultaneously unlike micrometers and calipers which measure one dimension at a time.
Fifth, optical comparators are easy to use. Even those without much gauging experience can make accurate measurements using the device. Sixth, optical comparators are non-contact gages. This ensures that nothing but light touches a part during measurement. The property greatly minimizes the possibility of any change in the shape of the delicate parts which could arise from any direct force during the process. Non-contact gage also eliminates the “feel factor” and resulting human error of hand gages. Finally, the device is more suitable for precision measurement as it gives higher magnification and contains less movable parts.
Benefit from Our Service: Save 25% Along with the first order offer - 15% discount, you save extra 10% since we provide 300 words/page instead of 275 words/page
Disadvantages of Optical Comparators
For illumination operation of the optical comparators to be possible, there must be an external power source. Second, the apparatus are also of comparatively large size and are costly (Kulkarni, 2009). Finally, optical comparators unlike video measurement systems lucks properties like: image processing capabilities, variable zoom lens systems, color, and profile images. The video measuring systems allow a computer measurement program to compare images down to pixel level for ultra-accurate measurement. These video systems are also quick and allow for 3 axis surface and dimensional mapping of samples with extreme preciseness. The optical comparator is not able to capture image of inspected part. It will thus obviously be superseded by video measurement systems.